|
Post by bowhntr66 on Sept 30, 2013 3:25:30 GMT -5
Wow!! I really like that!!! He's awesome!!
|
|
|
Post by mikedeco on Sept 30, 2013 5:40:30 GMT -5
Excellent project, great design and really well executed, the articulations seems to work fine. A true labor of love. Would really like to see more images of the 3D printed parts. Did you put it together with the prototype or you had the patience to wait to have all the parts cast is resin? Big big congrats on this inspiring project.
|
|
|
Post by tsamtsam28 on Sept 30, 2013 10:14:02 GMT -5
the last pic is a badass pose!
|
|
|
Post by xiombarg on Sept 30, 2013 11:50:41 GMT -5
Thanks guys. I originally printed the entire leg portion in an inexpensive material and put it together to test the joints. With the inverted leg (or whatever you call it) and the large upper body, the whole thing needs heavy duty joints. Though these look like regular hinges there is actually a small nylon lock nut imbedded in every articulation point to give it just the right amount of tension. The nylon can take a lot of movement without wearing down. I'll post up some pictures to show how I made these later.
I wish I would have printed the entire thing in a cheap material first. It would have saved me some money from unforeseen design issues, but I didn't put anything else together besides the leg until after I had cast them.
|
|
|
Post by boma83 on Sept 30, 2013 16:20:11 GMT -5
man! that is Superb! great job
|
|
|
Post by xiombarg on Sept 30, 2013 20:22:46 GMT -5
man! that is Superb! great job Thanks!
|
|
|
Post by xiombarg on Oct 1, 2013 0:42:58 GMT -5
Excellent project, great design and really well executed, the articulations seems to work fine. A true labor of love. Would really like to see more images of the 3D printed parts. Did you put it together with the prototype or you had the patience to wait to have all the parts cast is resin? Big big congrats on this inspiring project. I'll post up some pics of the 3D parts this weekend.
|
|
|
Post by mikedeco on Oct 1, 2013 3:05:02 GMT -5
Cool thanks a lot
|
|
|
Post by xiombarg on Oct 5, 2013 12:57:01 GMT -5
Here are a few pics that show the 3D printed parts and how I used lock-nuts to strengthen all the joints. Harbor Freight is a great place to get inexpensive storage trays like these. These help me keep everything organized and keep them from chipping. 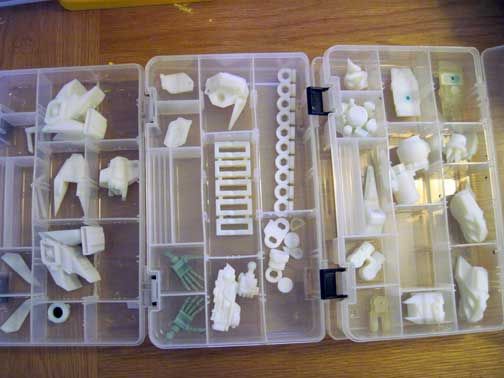 All these parts have been sanded. Sanding is a huge chore for a project like this and I learned real quick what works. My sandpaper of choice is Gator Adhesive backed yellow colored paper 220 grit. I buy the paper that is made for power sanding discs because it comes in bulk and it's cheap and effective. I don't like resin enhanced paper. Resin does last longer, but it doesn't sand well because the little granules on the paper aren't as sharp being covered in resin. Adhesive backed paper allows for anything to become a sanding utensil. I have various small and very stiff sheet metal shapes, tubes, square tubes etc. that I stick my paper onto that allow me to sand even in the tiniest areas. For the bigger areas I use an Iso-Tip Corded Filer/Sander. The adhesive paper works well for this tool also. 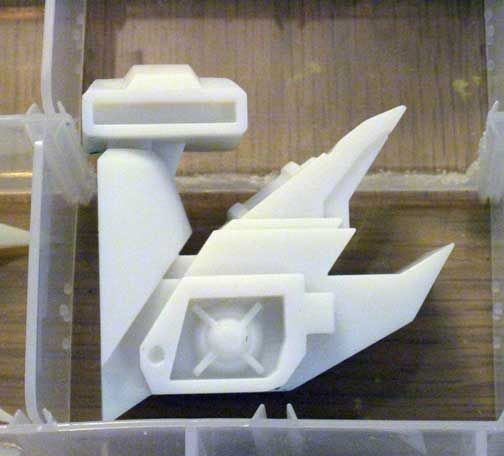 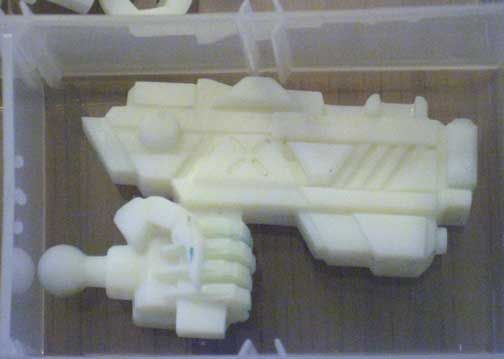 Here you can see how I modeled the parts to fit a locknut which I then glue into the final cast pieces using Gorilla Superglue (NOT regular Gorilla glue) which is a vinyl based superglue and not a cyanoacrylate like most superglue. Vinyl rubber based glues allows metal to glue to plastic and hold firm unlike cyanoacrylate superglues. The locknuts could probably be Epoxied in as well but epoxy is a little harder to control without getting messy. 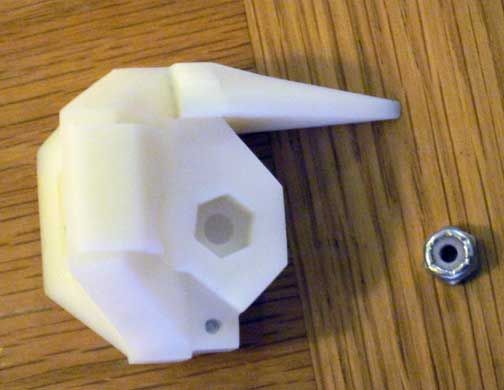 Here's a pic of a locknut connection point (note that the threading faces the exposed side; if you do it the other way you will have problems getting your screw in) The benefit of locknuts is that they have a nylon gasket which is an extremely resilient material that doesn't powder and weaken like most plastics. Locknuts come in lots of sizes depending on how much tension you need. I use a #6-32 for most joints and on this figure. 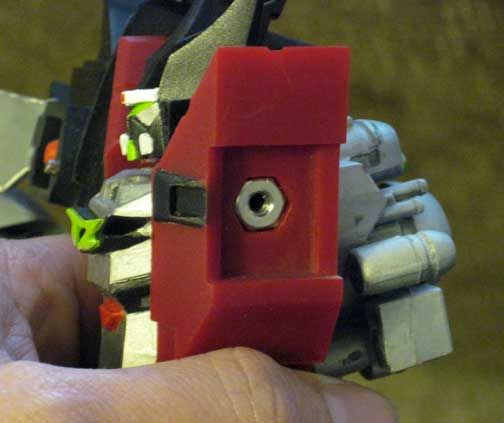
|
|
|
Post by magengar on Oct 5, 2013 13:25:27 GMT -5
WOW!!!!!!!!!!!! Your test figure looks AWESOME!!! You should get it patented and copyrighted so you can own all the rights to it. It definitely deserves its very own anime and manga!  And, with Harbor Freight, ya Can't go wrong!  There's a Harbor Freight store a few miles up the road from me. zozo-mag
|
|
|
Post by bowhntr66 on Oct 5, 2013 13:28:22 GMT -5
Wow, great attention to detail!! One other thing you may not have known about regular Gorilla Glue, it swells when drying. I know people that have tried to use it to glue countertops down and had to trash the project. Ever since then, the reps make us warn about the swelling to everyone that buys it from our store.
|
|
|
Post by magengar on Oct 5, 2013 13:30:54 GMT -5
True, Gorilla Glue does indeed swell when drying. Under some circumstances you can use that swelling to a creative advantage.  zozo-mag
|
|
|
Post by xiombarg on Oct 5, 2013 15:16:11 GMT -5
WOW!!!!!!!!!!!! Your test figure looks AWESOME!!! You should get it patented and copyrighted so you can own all the rights to it. It definitely deserves its very own anime and manga!  And, with Harbor Freight, ya Can't go wrong!  There's a Harbor Freight store a few miles up the road from me. zozo-mag Thanks man. I'm slowly and painfully working on a comic book, which at my current rate should be out in about ten billion years or so... no but seriously, it should be completely finished and printed within about six months barring any unforeseen holdups. I've got the whole thing penciled and I'm working on inks at the moment. Not sure if I'll be able to do it in color. Having to do the whole thing myself is a lot to take on so it will probably be B&W to save on costs. Harbor Freight is great for inexpensive stuff. Not sure about their power tools though. When I resin cast I do pressure casting using pressure pots and Harbor Freight has really inexpensive, relatively well made pressure containers for the price. If you use their 20% off coupons they only cost about $80, which is about $200-$300 less than most other pressure containers.
|
|
|
Post by xiombarg on Oct 5, 2013 15:19:16 GMT -5
Wow, great attention to detail!! One other thing you may not have known about regular Gorilla Glue, it swells when drying. I know people that have tried to use it to glue countertops down and had to trash the project. Ever since then, the reps make us warn about the swelling to everyone that buys it from our store. I don't know what people use regular Gorilla Glue for? I haven't found anything I can use it for because of how messy it is.
|
|
|
Post by magengar on Oct 5, 2013 16:24:53 GMT -5
The first time I discovered Harbor Freight was at a Tool flea-market which they hosted in my area several years ago. At that time I bought a small bench grinder from them (paid $35 for it, New!) and it lasted me a very good while before I sold it. I'm thinking of getting another one from them, as well as an orbital sander, anytime soon now that I have a much bigger space to work in for my custom jobs. zozo-mag WOW!!!!!!!!!!!! Your test figure looks AWESOME!!! You should get it patented and copyrighted so you can own all the rights to it. It definitely deserves its very own anime and manga!  And, with Harbor Freight, ya Can't go wrong!  There's a Harbor Freight store a few miles up the road from me. zozo-mag Thanks man. I'm slowly and painfully working on a comic book, which at my current rate should be out in about ten billion years or so... no but seriously, it should be completely finished and printed within about six months barring any unforeseen holdups. I've got the whole thing penciled and I'm working on inks at the moment. Not sure if I'll be able to do it in color. Having to do the whole thing myself is a lot to take on so it will probably be B&W to save on costs. Harbor Freight is great for inexpensive stuff. Not sure about their power tools though. When I resin cast I do pressure casting using pressure pots and Harbor Freight has really inexpensive, relatively well made pressure containers for the price. If you use their 20% off coupons they only cost about $80, which is about $200-$300 less than most other pressure containers.
|
|
|
Post by xiombarg on Oct 5, 2013 21:45:01 GMT -5
I think their basic power tools and most hand tools are probably fairly reliable. There are customer reviews of all their stuff on their web site, so that's good. I've actually found a number of useful tools and items that I wouldn't have thought of otherwise if I hadn't seen them on the shelves at Harbor Freight. The first time I discovered Harbor Freight was at a Tool flea-market which they hosted in my area several years ago. At that time I bought a small bench grinder from them (paid $35 for it, New!) and it lasted me a very good while before I sold it. I'm thinking of getting another one from them, as well as an orbital sander, anytime soon now that I have a much bigger space to work in for my custom jobs. zozo-mag Thanks man. I'm slowly and painfully working on a comic book, which at my current rate should be out in about ten billion years or so... no but seriously, it should be completely finished and printed within about six months barring any unforeseen holdups. I've got the whole thing penciled and I'm working on inks at the moment. Not sure if I'll be able to do it in color. Having to do the whole thing myself is a lot to take on so it will probably be B&W to save on costs. Harbor Freight is great for inexpensive stuff. Not sure about their power tools though. When I resin cast I do pressure casting using pressure pots and Harbor Freight has really inexpensive, relatively well made pressure containers for the price. If you use their 20% off coupons they only cost about $80, which is about $200-$300 less than most other pressure containers.
|
|
|
Post by magengar on Oct 6, 2013 0:18:20 GMT -5
Yep, it helps to go into their store to see the tools up close and in hand. Whenever I go there I get googley-eyed at all the eye-candy of tools and gadgets in the aisles. lol  zozo-mag
|
|
|
Post by mikedeco on Oct 7, 2013 15:27:20 GMT -5
Thanks for sharing the picts and infos. Sanding is indeed the most painfull part of the process. If I wasn't as maniac as I am, I think I would do a lot more projects, it's just that I have between 40 and 60 hours of sanding on my projects each time and it's always hard to sit down and sand for hours.
It's hard to see on your picts what kind of printer you've been using. I'm pretty happy with SLA printer for the moment and I use wet sanding, it's working well and you use a lot less sandpaper for a great result. But I usually go for a 240 grid first, then 400 and I finish sometimes with a 600.
Congrats again as your project shows a lot of love and dedication. Thanks again for sharing.
|
|
|
Post by xiombarg on Oct 7, 2013 21:10:43 GMT -5
Thanks for sharing the picts and infos. Sanding is indeed the most painfull part of the process. If I wasn't as maniac as I am, I think I would do a lot more projects, it's just that I have between 40 and 60 hours of sanding on my projects each time and it's always hard to sit down and sand for hours. It's hard to see on your picts what kind of printer you've been using. I'm pretty happy with SLA printer for the moment and I use wet sanding, it's working well and you use a lot less sandpaper for a great result. But I usually go for a 240 grid first, then 400 and I finish sometimes with a 600. Congrats again as your project shows a lot of love and dedication. Thanks again for sharing. Sanding is probably the most tedious part of the whole process. I sand while watching TV. I just set up a garbage can, turn on the tube and sand away. I've probably watched the entire runs of The Office and Seinfeld three or four times. But I've become less fanatical about my sanding after trying Krylon Crystal Clear satin acrylic coat. This stuff hides a lot of texture, scratches and surface imperfections because of how it disperses light. It's fantastic stuff for projects like these. I don't have my own printer, but my stuff is printed on an Objet printer. I'm not sure what resolution settings my service uses, but I know that Objet's are capable of printing within 20 microns. I always thought Objet's were SLA printers, but I was told that they use their own printing process.
|
|
|
Post by xiombarg on Oct 13, 2013 23:20:18 GMT -5
I'm trying out a new printing service. Ponoko raised their prices awhile ago and I've now found www.imaterialise.com has by far the best pricing for high resolution prints that I've yet found. From what I've read they've been around for more than a decade and do the 3D print work for just about everybody in commercial prototyping. They are located in Europe, but their shipping in extremely reasonable.
|
|